Did you know that a single contaminated sterile product could jeopardize patient safety and potentially cost millions in recalls? That’s where Container Closure Integrity Testing (CCIT) comes in. As a QA manager or validation engineer in the pharmaceutical industry, you’re likely familiar with the critical role CCIT plays in ensuring product safety and regulatory compliance.
CCIT is essential for maintaining the sterility of drugs, medical devices, and biologics throughout their shelf life. It’s not just about meeting FDA requirements; it’s about safeguarding your product’s integrity and your company’s reputation. In this article, we’ll explore the latest CCIT methods, their benefits, and how they can streamline your quality assurance processes.
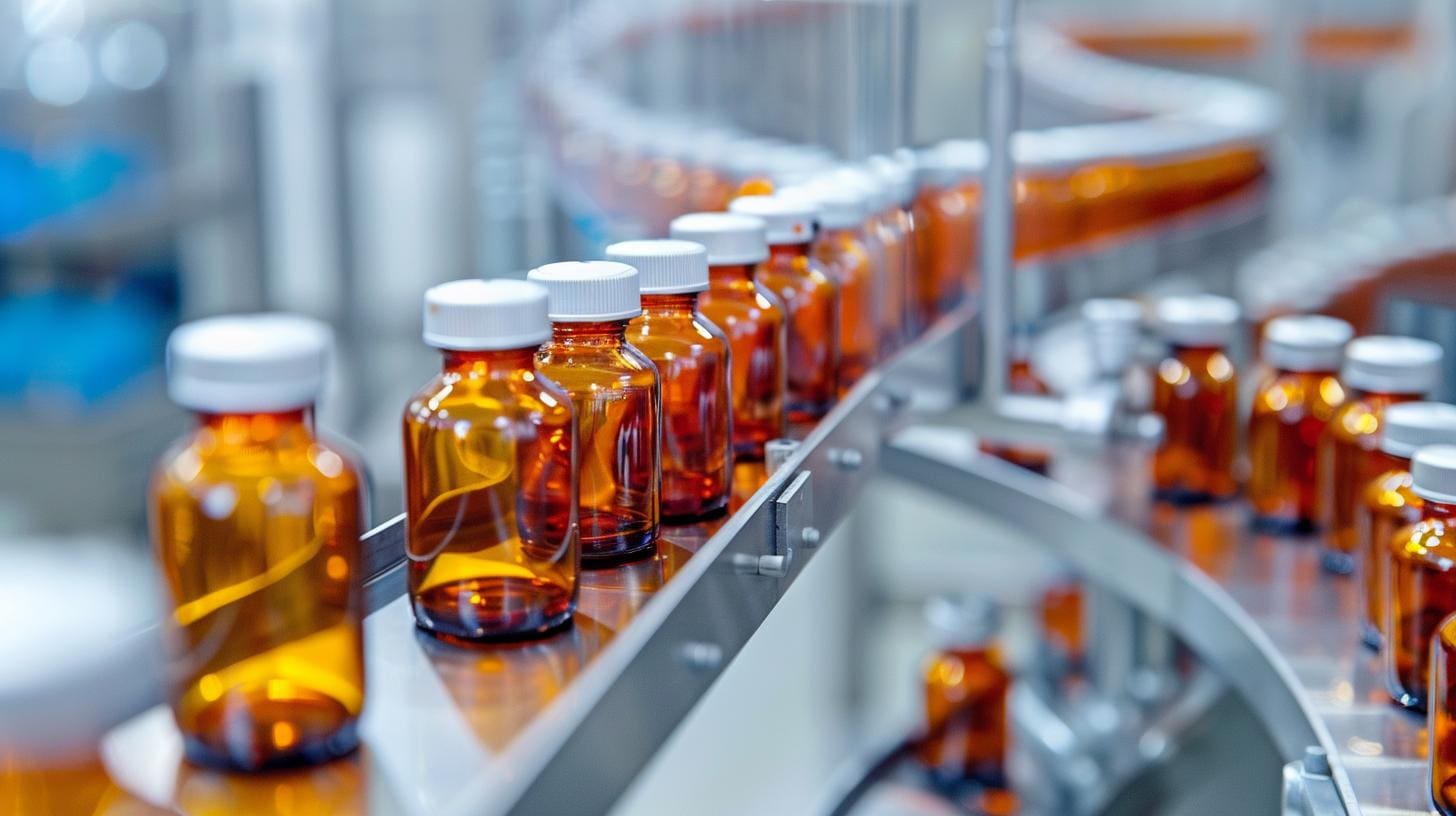
Introduction to CCIT for Sterile Products
Container Closure Integrity Testing (CCIT) is a crucial process in pharmaceutical packaging that ensures product sterility and quality. This section explores the fundamentals of CCIT, its significance in pharmaceutical packaging, and an overview of sterile products.
Defining CCIT
CCIT is a comprehensive testing method designed to detect breaches in container closure systems that could compromise product sterility. It involves evaluating the seal integrity of primary packaging components, such as vials, syringes, and ampules. CCIT methods include vacuum decay, helium leak detection, and high-voltage leak detection, each tailored to specific packaging types and product requirements.
The Importance of CCIT in Pharmaceutical Packaging
CCIT plays a vital role in maintaining product safety and regulatory compliance. FDA studies indicate packaging-related issues account for 22% of drug recalls in the United States. Implementing effective CCIT procedures significantly reduces contamination risks, enhances patient safety, and protects brand reputation. CCIT also helps pharmaceutical companies meet stringent regulatory requirements, including FDA guidelines and cGMP standards.
Overview of Sterile Products
Sterile products encompass injectable drugs, ophthalmic solutions, and intravenous fluids. These products are highly susceptible to microbial contamination, making robust packaging and testing processes essential. Sterile products require aseptic manufacturing conditions and specialized container closure systems to maintain integrity throughout their shelf life. CCIT ensures these products remain sterile from production to patient administration, safeguarding efficacy and safety.
Understanding Sterile Pharmaceutical Products
Sterile pharmaceutical products are critical components of modern healthcare, requiring rigorous manufacturing processes and testing to ensure patient safety. These products must remain free from microbial contamination throughout their lifecycle, from production to administration.
Types of Sterile Products
Sterile injectable drugs dominate the market, valued at $357.7 billion in 2020 with a projected 7.5% CAGR through 2028. Ophthalmic solutions follow, reaching $28.4 billion in 2020. Intravenous fluids are expected to hit $15.2 billion by 2027. These products include:
- Injectable medications (antibiotics, vaccines)
- Ophthalmic preparations (eye drops, contact lens solutions)
- Intravenous fluids and parenteral nutrition
- Inhaled medications (nebulizer solutions)
Challenges in Maintaining Sterility
Maintaining product sterility is a complex task fraught with potential pitfalls:
- Container closure design flaws
- Manufacturing defects
- Transportation and storage damage
- Human error in aseptic techniques
- Inadequate environmental monitoring
The Parenteral Drug Association (PDA) reports human error as the leading cause of sterility failures. Proper training, robust quality control systems, and advanced container closure integrity testing (CCIT) methods are essential to mitigate these risks.
Consequences of Sterility Breaches
Sterility failures can have devastating consequences:
- Patient infections and potential fatalities
- Product recalls and financial losses
- Regulatory penalties and legal liabilities
- Damage to brand reputation and consumer trust
A stark example occurred in 2012 when contaminated injectable steroids from a U.S. compounding pharmacy caused a fungal meningitis outbreak. The incident resulted in 64 deaths and 793 infections, underscoring the critical importance of stringent sterility maintenance and testing protocols in pharmaceutical manufacturing.
CCIT Methods for Sterile Products
Container Closure Integrity Testing (CCIT) employs various methods to ensure the sterility of pharmaceutical products. Each technique offers unique advantages for detecting leaks and maintaining product integrity.
Vacuum Decay
Vacuum decay testing detects leaks as small as 5 µm in diameter. It’s ideal for rigid and semi-rigid containers, offering sensitivity up to 10-6 mbar·L/s. This method creates a vacuum around the container and measures pressure changes, indicating potential breaches in the packaging.
High Voltage Leak Detection (HVLD)
HVLD identifies leaks down to 0.5 µm in diameter, making it suitable for conductive containers like glass vials and syringes. With a sensitivity of 0.4 µm, this method applies an electrical current to detect defects in the container’s structure or seal.
Headspace Gas Analysis
For containers with headspace, such as vials and syringes, headspace gas analysis detects leaks as small as 0.1 µm. This technique analyzes the composition of gases within the container to identify potential breaches, offering a sensitivity of 0.4 µm.
Helium Leak Detection
Helium leak detection boasts high sensitivity, identifying leaks as small as 0.1 µm in diameter. It’s versatile, suitable for various container types, and offers sensitivity up to 10-10 mbar·L/s. This method uses helium as a tracer gas to detect even the smallest leaks in packaging.
Laser-Based Headspace Analysis
Non-destructive and suitable for 100% in-line testing, laser-based headspace analysis detects leaks down to 0.3 µm in diameter. With a sensitivity of 0.4 µm, this method uses laser technology to analyze the headspace composition, ensuring container closure integrity without compromising the product.
Regulatory Landscape for CCIT of Sterile Products
Container closure integrity testing (CCIT) for sterile products is subject to stringent regulatory requirements. These regulations ensure product safety and efficacy throughout its shelf life. Let’s explore the key regulatory bodies and their guidelines for CCIT.
FDA Requirements
The FDA’s Guidance for Industry outlines specific expectations for CCIT methods and validation. It emphasizes the importance of using validated CCIT methods as an alternative to sterility testing in stability protocols. The guidance recommends:
- Selecting appropriate CCIT methods based on product characteristics
- Validating CCIT methods to demonstrate sensitivity, specificity, and reproducibility
- Establishing acceptance criteria for CCIT results
- Incorporating CCIT into stability testing programs
EU GMP Guidelines
EU GMP Annex 1 mandates secure container closure systems for sterile medicinal products. Key requirements include:
- Implementing appropriate CCIT methods during product development and manufacturing
- Validating CCIT methods to ensure they can detect breaches in container integrity
- Conducting CCIT at various stages of the product lifecycle, including stability testing
- Maintaining documentation of CCIT results and method validation
USP <1207> Guidelines
USP <1207> provides comprehensive guidance on CCIT method selection and validation. The chapter covers:
- Deterministic vs. probabilistic CCIT methods
- Risk-based approach to CCIT method selection
- Validation requirements for different CCIT technologies
- Considerations for method transfer and routine testing
How do these regulatory guidelines impact your CCIT strategy for sterile products?
Best Practices for CCIT in Sterile Product Manufacturing
Implementing effective Container Closure Integrity Testing (CCIT) practices is crucial for ensuring the safety and quality of sterile products. These best practices encompass various aspects of the manufacturing process, from production line integration to staff training.
Integrating CCIT into Production Lines
Automated CCIT systems integrated into production lines enable 100% inspection of sterile drug containers. This approach ensures consistent quality control and reduces the risk of contamination. For example, Pfizer’s automated CCIT system uses high-speed cameras and machine learning algorithms to detect defects in vial seals at rates up to 600 units per minute.
Determining Testing Frequency
CCIT frequency varies based on product and packaging type. A combination of in-process and final product testing provides optimal sterility assurance. For high-risk products, such as injectable biologics, manufacturers typically perform CCIT at multiple stages:
- After filling and sealing
- Post-lyophilization (if applicable)
- Before final packaging
- During stability testing
Managing Failed Containers
Containers failing CCIT require immediate segregation and investigation. Implement a robust root cause analysis process to identify failure sources:
- Isolate failed containers
- Document failure details (date, time, batch number)
- Perform visual inspection
- Conduct additional non-destructive tests
- Analyze data for trends or patterns
Use findings to improve manufacturing processes and prevent future failures.
Staff Training and Qualification
Comprehensive CCIT operator training is essential for maintaining testing integrity. Develop a training program that includes:
- Theoretical knowledge of CCIT principles
- Hands-on experience with specific equipment
- Method validation procedures
- Data interpretation and reporting
- Troubleshooting common issues
Conduct regular competency assessments and refresher training to ensure operators maintain proficiency with evolving CCIT technologies and regulatory requirements.
Challenges and Considerations in CCIT for Sterile Products
Container Closure Integrity Testing (CCIT) for sterile products presents unique challenges that require careful consideration. Manufacturers must navigate complex decisions to ensure product safety and regulatory compliance while maintaining operational efficiency.
Selecting Appropriate CCIT Methods
CCIT method selection depends on container type, product characteristics, and required sensitivity. Vacuum decay testing works well for rigid containers, while high voltage leak detection suits non-conductive materials. Laser-based headspace analysis excels for transparent containers. Consider your production process compatibility when choosing a method. For example, a pharmaceutical company producing sterile injectables in glass vials might opt for vacuum decay testing due to its high sensitivity and non-destructive nature.
Balancing Sensitivity and Specificity
CCIT methods’ false positive rates range from 0.1% to 1%, while false negatives occur at 0.01% to 0.1%. High sensitivity detects potential leaks but may increase false rejects, impacting production costs. A biotech firm manufacturing high-value biologics might prioritize sensitivity to ensure product integrity, accepting a higher false positive rate. In contrast, a large-scale vaccine producer might seek a balance to maintain production efficiency.
Cost Considerations
CCIT equipment investments range from $100,000 to over $1 million. These costs pale in comparison to potential product recalls or sterility failures, which can cost millions. A mid-sized pharmaceutical company investing in a $500,000 CCIT system might recoup costs by preventing a single major recall. Consider long-term savings from reduced quality control issues and improved regulatory compliance when evaluating CCIT investments.
Handling False Positives and Negatives
Minimize false results through proper equipment maintenance, regular calibration, and appropriate controls. When false results occur, conduct thorough investigations to identify root causes. For instance, a false positive in vacuum decay testing might result from improper container placement. Implement corrective actions, such as improved operator training or equipment adjustments, to prevent recurrence and maintain testing integrity.
Future Trends in CCIT for Sterile Products
Container closure integrity testing (CCIT) for sterile products is rapidly evolving, driven by technological advancements and increasing regulatory demands. These emerging trends are reshaping the landscape of pharmaceutical manufacturing and quality control.
Emerging Technologies
Advanced imaging techniques are revolutionizing CCIT for sterile products. X-ray computed tomography (CT) provides high-resolution 3D images of container closure systems, detecting micro-defects invisible to the naked eye. Optical coherence tomography (OCT) offers non-destructive, real-time analysis of package integrity, enabling manufacturers to identify potential breaches without compromising product sterility. These technologies enhance the sensitivity and specificity of CCIT, reducing false positives and negatives in sterility testing.
Automation and AI in CCIT
Artificial intelligence (AI) and machine learning algorithms are transforming CCIT processes. AI-powered systems analyze vast amounts of data from multiple testing methods, identifying patterns and anomalies with greater accuracy than human operators. Machine learning algorithms adapt to different container types and product characteristics, optimizing testing parameters for each unique application. This automation reduces human error, increases throughput, and improves the overall efficiency of CCIT in pharmaceutical manufacturing.
Potential for Real-Time, Continuous Monitoring
Innovative sensor technologies are paving the way for continuous, real-time monitoring of container closure integrity. Smart packaging solutions incorporate miniaturized sensors that detect changes in pressure, humidity, or gas composition within the container. These systems provide instant alerts of potential breaches, allowing for immediate corrective actions. Blockchain technology integrates with these sensors, creating an immutable record of a product’s integrity throughout its lifecycle, from manufacturing to patient use.
CCIT Future Trend | Key Benefits |
---|---|
Advanced Imaging | High-resolution defect detection, Non-destructive testing |
AI and Automation | Improved accuracy, Increased efficiency, Reduced human error |
Real-Time Monitoring | Instant breach detection, Continuous integrity assurance |
Conclusion: The Future of CCIT in Sterile Product Manufacturing
CCIT for sterile products is evolving rapidly, driven by technological advancements and stricter regulatory requirements. As you adapt to these changes, you’ll find that innovative methods like advanced imaging techniques and AI-powered systems are revolutionizing the field.
These developments promise enhanced accuracy, efficiency, and real-time monitoring capabilities. By embracing these new technologies, you’ll be better equipped to ensure product integrity and patient safety. Stay informed about emerging trends and be ready to integrate cutting-edge solutions into your CCIT processes to maintain a competitive edge in the pharmaceutical industry.